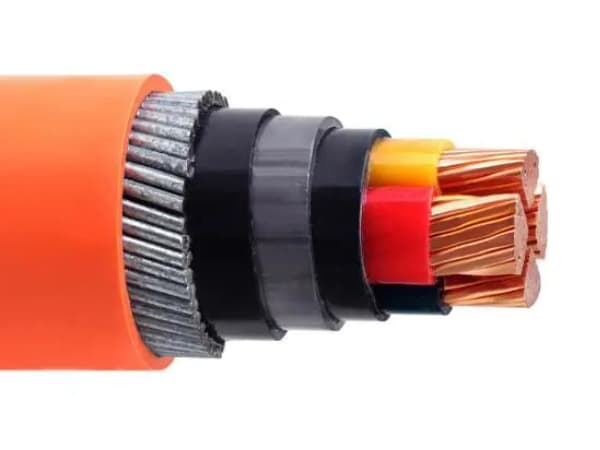
In the world of electrical engineering and telecommunications, lead sheath cables have carved out a niche due to their unique characteristics and historical significance. These cables are renowned for their durability, environmental resistance, and protective features. This article will delve into the various aspects of lead sheath cables, including their components, অ্যাপ্লিকেশন, and how to find the right lead sheath cable for sale or lead sheath cable manufacturer. We will also explore specific types of lead sheath cables such as lead sheathed telephone cables and paper insulated lead sheathed cables.
What is Lead Sheath Cable?
ক lead sheath cable is a type of electrical cable characterized by its outer protective layer made of lead. This design offers several benefits, particularly in environments where cables are exposed to harsh conditions. The lead sheath provides robust protection against mechanical damage, আর্দ্রতা, and various chemical substances, making it suitable for both indoor and outdoor applications.
Components of Lead Sheath Cable
- কন্ডাক্টর: The core component of the cable, typically made from copper or aluminum, which conducts the electrical current.
- Insulation: Surrounding the conductor, this layer is made from materials such as rubber or plastic and prevents electrical leakage, ensuring safety and efficiency.
- Lead Sheath: The outermost layer made of lead, offering protection against external elements, physical damage, and environmental factors.
Advantages of Lead Sheath Cable
1. Superior Durability
The primary advantage of lead sheath cables is their durability. The lead sheath acts as a strong physical barrier, protecting the inner conductor and insulation from mechanical damage and wear. This makes these cables ideal for installations in areas where physical stress or impact is a concern.
2. Excellent Environmental Protection
Lead sheathed cables are highly resistant to environmental factors such as moisture, রাসায়নিক, and extreme temperatures. The lead sheath provides a waterproof barrier that prevents water ingress, which is crucial for maintaining the integrity and performance of the cable over time.
3. Longevity
Given their robust construction, lead sheath cables are known for their longevity. They are designed to withstand harsh conditions and continue functioning effectively for many years, which can be a significant advantage in long-term installations.
4. Historical Provenance
Lead sheath cables have been used for over a century, particularly in telecommunications and power distribution. Their proven track record in various applications lends confidence in their continued use, especially in legacy systems and specialized applications.
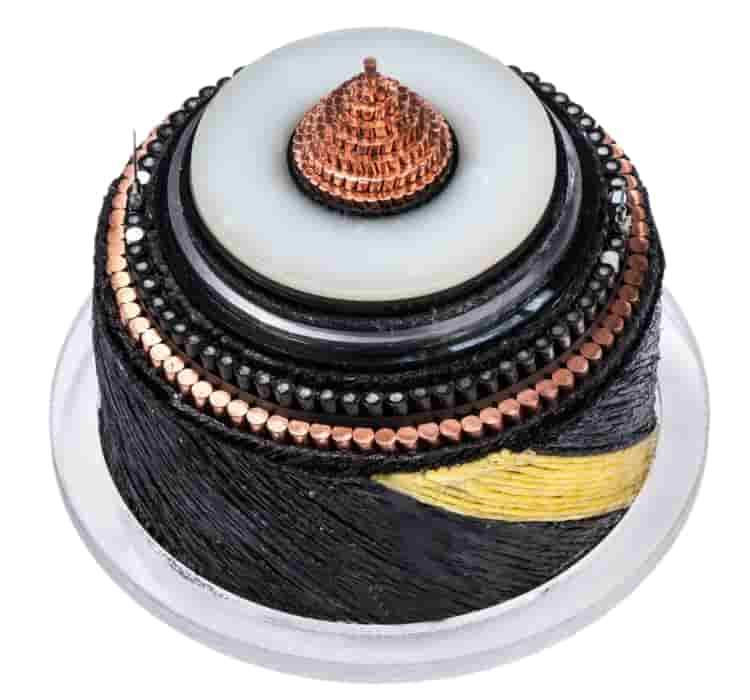
Lead Sheathed Telephone Cable
One of the notable applications of lead sheath cables is in lead sheathed telephone cables. Historically, these cables were a standard choice for telephone networks due to their ability to protect delicate telephone signals from external interference and environmental damage.
Characteristics of Lead Sheathed Telephone Cables
Signal Protection: The lead sheath shields the cables from external electromagnetic interference, ensuring clearer signal transmission and reducing noise.
Durability: These cables are designed to withstand physical stresses and environmental conditions, making them suitable for both indoor and outdoor use.
Legacy Systems: While modern cables have largely replaced lead sheathed telephone cables, they are still found in older telephone systems and may require maintenance or replacement.
Paper Insulated Lead Sheathed Cable
Another variant of lead sheath cables is the paper insulated lead sheathed cable. This type combines paper insulation with a lead sheath, offering distinct advantages in certain applications.
Benefits of Paper Insulated Lead Sheathed Cable
Enhanced Insulation: The paper insulation provides excellent electrical insulation, which helps maintain the integrity of the electrical signal and prevents leakage.
Historical Usage: Paper insulated lead sheathed cables were widely used in the early 20th century and remain in use in specific applications where their unique properties are beneficial.
Applications of Lead Sheathed Wire
Power Transmission: These cables are often used in power transmission networks where long-term reliability and protection from environmental factors are essential.
Specialized Industrial Use: In certain industrial applications, the combination of paper insulation and a lead sheath provides the necessary durability and protection.
Lead Sheath Cable for Sale
When searching for lead sheath cable for sale, it’s important to consider several factors to ensure you find the right product for your needs.
1. Determine Your Requirements
Type of Cable: Identify whether you need a standard lead sheath cable, a paper insulated lead sheathed cable, or a specific type for a particular application.
Specifications: Consider the length, diameter, and other technical specifications required for your project.
2. Quality and Compliance
Certifications: Ensure that the cables meet industry standards and certifications for quality and safety. This is crucial for ensuring reliable performance and compliance with regulations.
Manufacturer Reputation: Choose products from reputable manufacturers known for their quality and reliability. This helps avoid issues related to defective or substandard cables.
3. Cost Considerations
Pricing: Compare prices from different suppliers to get a competitive rate. Keep in mind that higher prices do not always guarantee better quality, so balance cost with other factors such as quality and reliability.
Budget: Plan your budget, including any additional costs for shipping and installation. Consider both initial costs and long-term value when making your decision.
Manufacturing Lead Sheath Cable Processing
In the vast landscape of electrical cable manufacturing, lead sheath cables occupy a unique niche due to their exceptional resistance to corrosion, আর্দ্রতা, and mechanical damage. Commonly used in underground power distribution systems, telecommunications, and even nuclear power plants, lead sheath cables are engineered to withstand harsh environments and ensure reliable performance over extended periods. This article delves into the intricate manufacturing process of lead sheath cables, highlighting the key steps, materials involved, and the technology that drives this precision craft.
Introduction
Lead sheath cables are characterized by their outer layer of lead alloy, which not only provides protection against environmental factors but also acts as a shield against electromagnetic interference (ইএমআই) and radiofrequency interference (RFI). The inner core, comprising conductors insulated with various materials, carries the electrical signal or power. The manufacturing process of lead sheath cables is a meticulous blend of traditional craftsmanship and advanced machinery, ensuring the highest standards of quality and safety.
উপাদান নির্বাচন
The first step in the manufacturing process involves meticulous material selection. The conductors, typically made of high-purity copper or aluminum, are chosen for their excellent electrical conductivity and durability. The insulation material, often polyethylene or PVC, is selected for its resistance to heat, আর্দ্রতা, এবং রাসায়নিক. The lead sheath itself is composed of a lead alloy, typically a blend of lead with other metals like tin or antimony, to enhance its mechanical strength and corrosion resistance.
Conductor Manufacturing
The selected copper or aluminum wire is drawn through a series of progressively smaller dies to achieve the desired diameter and stranding configuration. This process, known as wire drawing, ensures that the conductors are uniform in size and shape, critical for efficient current flow and mechanical strength. The drawn wires are then stranded into a bundle, using either a concentric or sectoral stranding pattern, to increase flexibility and reduce the likelihood of breakage under tension.
Insulation Application
Once the conductors are ready, the insulation material is extruded over them. This is typically done using an extrusion machine, where the molten insulation material is forced through a die surrounding the conductor bundle. The extrusion process forms a seamless, uniform layer of insulation around each conductor, protecting it from electrical shorts and environmental hazards.
Assembling the Cable Core
The insulated conductors are then assembled into the cable core, often with additional fillers and binders to maintain the shape and position of the conductors. The fillers ensure that the cable maintains a circular cross-section, while the binders help hold the components together during subsequent manufacturing steps.
Lead Sheath Application
The lead sheath is applied over the cable core in a controlled environment to prevent contamination. This step typically involves extruding or casting the lead alloy around the cable core, ensuring a tight, continuous layer of protection. The lead sheath is then sealed at both ends to prevent moisture ingress and maintain the cable’s integrity.
Testing and Quality Control
Throughout the manufacturing process, rigorous testing and quality control measures are in place to ensure that the lead sheath cables meet or exceed industry standards. Electrical tests, such as continuity and insulation resistance checks, are performed to verify the cable’s performance. Physical tests, including bend and tensile strength evaluations, assess the cable’s mechanical durability. উপরন্তু, visual inspections and dimensional measurements ensure that the cables conform to design specifications.
Final Assembly and Packaging
Once the cables have passed all quality control checks, they undergo final assembly, which may include attaching connectors, terminations, or other accessories as required by the application. The cables are then carefully packaged to prevent damage during shipping and storage. Packaging materials are selected to provide adequate protection while also being environmentally friendly.
The manufacturing process of lead sheath cables is a complex endeavor that requires a blend of precision engineering, skilled labor, and rigorous quality control. From material selection to final assembly, every step is critical in producing cables that are reliable, safe, and long-lasting. As the demand for underground and harsh environment electrical infrastructure continues to grow, the importance of lead sheath cables and their manufacturing processes becomes increasingly apparent. With ongoing advancements in technology and materials science, the future of lead sheath cable manufacturing looks bright, promising even greater performance and versatility for these essential components of modern electrical systems.
Lead Sheath Cable Manufacturer
1. Experience and Expertise
Industry Experience: Look for manufacturers with a long history of producing lead sheath cables. Experienced manufacturers are likely to provide better quality products and support.
Technical Expertise: Ensure the manufacturer has the technical capabilities to meet your specific requirements, whether you need standard cables or customized solutions.
2. Product Range and Customization
Variety of Cables: A reputable manufacturer should offer a range of lead sheath cables, including different types and sizes to suit various applications.
কাস্টমাইজেশন বিকল্প: Check if the manufacturer offers customization options to tailor the cables to your specific needs. This could include custom lengths, insulation types, or other modifications.
3. Customer Reviews and References
Reviews: Look for customer reviews and testimonials to gauge the manufacturer’s reputation and reliability. Positive feedback from previous customers can indicate a trustworthy supplier.
References: Request references or case studies of past projects to understand the manufacturer’s capabilities and the quality of their products.
4. Support and Service
Customer Support: Choose a manufacturer that offers good customer support, including assistance with product selection, technical support, and after-sales service.
Warranty and Guarantees: Ensure the manufacturer provides warranties or guarantees on their products, which can provide additional peace of mind and protection.
Applications of Lead Sheath Cable
Lead sheath cable’s versatility and protective properties make it suitable for a wide range of applications across various industries. Some of the most common applications include:
Underground Power Distribution: PILC cables were once the standard for underground power distribution, providing a reliable and durable solution for transmitting electricity over long distances. While newer technologies have emerged, PILC cables still play a role in legacy systems and in specific circumstances where their properties are advantageous.
Telecommunications: Lead sheathed telephone cables have been instrumental in building the world’s telecommunications infrastructure. They are still used in some areas, particularly where reliability and durability are paramount.
Industrial Applications: Industries such as mining, oil and gas, and heavy manufacturing often require cables that can withstand harsh environments and heavy-duty use. Armored lead sheath cables are a popular choice for these applications, providing both electrical insulation and mechanical protection.
Nuclear Power Plants: In nuclear power plants, lead sheath cables are used for radiation shielding and other specialized purposes. Their ability to absorb and attenuate radiation makes them an essential component in ensuring the safety of personnel and equipment.
Custom Applications: Due to their customizable nature, lead sheath cables can be tailored to meet the unique requirements of specific applications or projects. This versatility allows them to be used in a wide range of settings, from marine environments to aerospace applications.
Professional lead Sheath cable manufacturer
We,ডোজেন্স ক্যাবল,lead sheath cable manufacturer, Lead sheath cables offer significant advantages in terms of durability, পরিবেশগত সুরক্ষা, and long-term reliability. Whether you are looking for lead sheath cable for sale, seeking a lead sheath cable manufacturer, or exploring options like lead sheathed telephone cables and paper insulated lead sheathed cables, understanding their characteristics and benefits will help you make informed decisions.
By considering factors such as cable specifications, quality, cost, and manufacturer reputation, you can ensure that you select the right lead sheath cable for your project. Whether for new installations or maintaining legacy systems, lead sheath cables continue to play a crucial role in various applications, providing reliable performance and protection in challenging environments.