Cable management is a critical aspect of modern infrastructure, ensuring that electrical cables are organized, accessible, and protected. Among the many solutions available, cable trays stand out for their versatility and efficiency. This comprehensive guide delves into everything you need to know about cable trays, including the different types, sizing considerations, and the top cable tray manufacturers and suppliers in the industry.
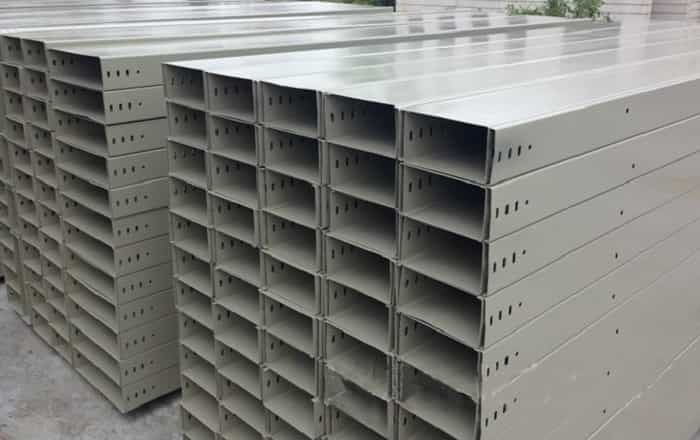
1. What is Cable Tray?
Cable trays are integral components in electrical systems, used to support insulated electrical cables. They provide a structured pathway for cables, facilitating installation, maintenance, and changes. Cable tray help in organizing cables and ensuring they are safely protected from physical damage and environmental factors.
2. Types of Cable Tray
There are several types of cable trays, each designed to meet specific needs:
2.1. Ladder Cable Tray
Ladder cable trays, also known as cable ladders, resemble a ladder with horizontal rungs. They are ideal for environments where ventilation is necessary, and they are often used for heavy-duty applications. The open design allows for easy access and cooling of cables.
2.2. Perforated Cable Tray
Perforated cable trays are similar to ladder trays but feature a solid base with perforations. This design supports smaller cables and provides moderate protection while still allowing for ventilation.
2.3. Solid Bottom Cable Tray
Solid bottom cable trays offer a continuous solid surface for cable support, making them suitable for environments where dust, debris, or other contaminants may be a concern. They provide excellent protection and are often used in industrial settings.
2.4. Wire Mesh Cable Tray
Wire mesh cable trays are made of woven or welded metal mesh. They are lightweight and provide flexibility in cable routing. These trays are often used in applications where easy modifications are required.
2.5. Cable Trunking
Cable trunking, sometimes referred to as cable ducts, is a type of cable management system that covers and protects cables. It is typically used in areas where aesthetics are a concern or where cables need to be concealed.
3. Key Benefits of Using Cable Tray
Cable tray offer numerous advantages for managing electrical systems:
Enhanced Cable Protection: They protect cables from physical damage and environmental factors.
Improved Safety: By organizing cables, they reduce tripping hazards and potential fire risks.
Ease of Maintenance: Cable trays facilitate easier access for inspection and maintenance.
Flexibility: They allow for easy modifications and expansions of electrical systems.
Cost-Effectiveness: They often prove to be a more economical solution compared to alternative cable management systems.
4. Cable Tray Sizing and Installation
Proper sizing and installation are crucial for the effective performance of cable trays:
4.1. Determining the Size
When selecting cable trays, it is essential to consider:
Cable Quantity and Size: The tray must accommodate the number and size of cables.
Load-Bearing Capacity: Ensure the tray can handle the weight of the cables and any additional loads.
Environmental Conditions: Consider factors like temperature, humidity, and exposure to chemicals or corrosive elements.
4.2. Installation Guidelines
Proper installation practices include:
Securing Trays: Ensure trays are securely mounted to prevent sagging or movement.
Maintaining Adequate Space: Allow enough space around cables for cooling and maintenance.
Following Regulations: Adhere to local electrical codes and standards during installation.
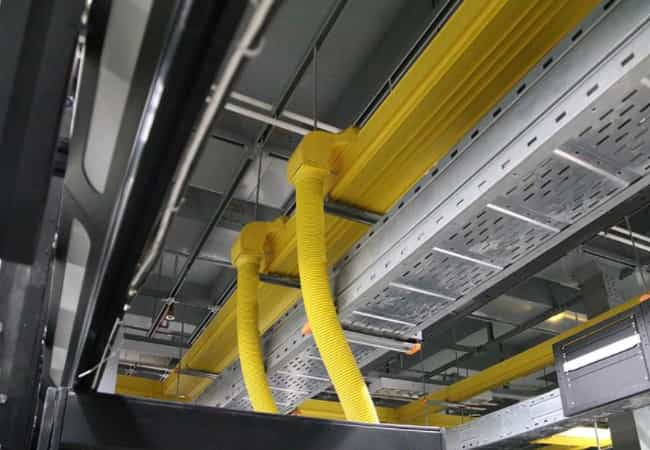
5. Choosing the Right Cable Tray Manufacturer
Selecting a reliable cable tray manufacturer is crucial for ensuring quality and performance. Here are some factors to consider:
5.1. Reputation and Experience
Look for manufacturers with a strong reputation and extensive experience in the industry. Established manufacturers are more likely to provide high-quality products and reliable support.
5.2. Product Range
A manufacturer offering a wide range of cable trays and related products can better meet diverse needs and preferences. Ensure they provide the specific type of tray you require.
5.3. Customization Options
For unique applications, customization might be necessary. Choose a manufacturer that offers custom solutions to meet your specific requirements.
5.4. Quality Assurance
Verify that the manufacturer adheres to industry standards and quality assurance processes. This ensures that the trays are durable and perform as expected.
As a cable tray supplier, Dosense Cable prides itself on delivering not just products but comprehensive electrical cable management systems tailored to specific project requirements. Our cable trays are designed to withstand the toughest conditions, ensuring safe and efficient cable routing in even the most challenging environments. From industrial factories to commercial complexes, hospitals, and data centers, our cable trays are trusted to support critical infrastructure with reliability and durability.
Extending our expertise beyond traditional cable trays, Dosense Cable is also a leading cable ladder supplier and manufacturer. Cable ladders, known for their open-frame design, offer exceptional ventilation and accessibility, making them ideal for applications where heat dissipation and easy maintenance are crucial. Our ladder type cable trays are manufactured with precision, using high-quality materials that ensure long-term performance and durability. Whether it’s a new installation or a retrofit project, our cable ladder solutions are designed to streamline cable management and optimize space utilization.
6.Design Considerations for Cable Tray Systems
When designing a cable tray system, several factors must be taken into account to ensure its functionality, safety, and cost-effectiveness.
6.1 Load Capacity
The first and foremost consideration is the load capacity of the tray. It must be able to support the weight of the cables, taking into account the number of cables, their diameter, and any additional accessories such as fasteners or brackets.
6.2 Material Selection:
Cable trays can be made from various materials, including steel, aluminum, stainless steel, and fiberglass-reinforced plastic (FRP). The choice depends on the application’s specific requirements, such as corrosion resistance, weight, and cost.
6.3 Environmental Conditions:
The tray’s material and design must withstand the environmental conditions it will be exposed to, including temperature, humidity, and exposure to chemicals or corrosive elements.
6.4 Fire Safety
In many applications, especially those in industrial settings, fire safety is a critical concern. Cable trays made from fire-resistant materials or equipped with fire-stopping devices can help mitigate the spread of fire.
6.5 Accessibility and Maintainability:
The tray design should facilitate easy access to cables for maintenance, repairs, or upgrades. Considerations such as spacing between rungs, tray width, and the inclusion of access panels can significantly impact maintenance efficiency.
6.6 Compliance with Standards and Regulations:
Cable tray systems must comply with relevant international and local standards and regulations, including those related to electrical safety, fire safety, and environmental considerations.
7. Installation Methods
The installation of cable trays involves several steps, ensuring compliance with safety standards and the intended purpose of the system. Here are the key aspects of cable tray installation:
7.1 Site Preparation:
Begin by assessing the site conditions, including the type of surface (e.g., concrete, metal decking), environmental factors (e.g., temperature, humidity), and accessibility.
Ensure the area is clear of obstacles and prepare the necessary tools and equipment.
7.2 Design and Layout:
Develop a detailed design plan, considering the route of the cables, the number and size of trays required, and the load-bearing capacity of the supports.
Mark the positions of the supports and trays on the floor or wall, using a laser level or other precision tools.
7.3 Support Installation:
Install the supports (or brackets) at the marked positions, ensuring they are securely fastened to the structure.
Check the alignment and levelness of the supports, adjusting as necessary to ensure a smooth and level tray run.
7.4 Tray Installation:
Assemble the cable trays according to the manufacturer’s instructions, connecting them end-to-end with appropriate fasteners.
Place the trays onto the supports, ensuring they are properly aligned and level.
Fasten the trays to the supports using appropriate hardware, such as bolts or clips.
7.5 Cable Installation:
Carefully route the cables and wires through the trays, following the design plan and ensuring they are properly supported and organized.
Use cable ties or other fasteners to secure the cables within the trays, maintaining proper spacing and avoiding overcrowding.
7.6 Inspection and Testing:
Perform a thorough inspection of the installed cable tray system, checking for any defects, loose connections, or non-compliance with the design plan.
Test the system to ensure it meets the required load-bearing capacity and functionality.
8. Stainless Steel Cable Tray vs PVC Cable Tray
When it comes to cable management systems, two of the most popular options are stainless steel cable trays and PVC (Polyvinyl Chloride) cable trays. Each has its unique set of advantages and is suitable for different applications. Here’s a comprehensive comparison of these two types of cable trays to help you make an informed decision.
8.1 Durability and Strength
Stainless steel cable trays are renowned for their exceptional durability and strength. Made from corrosion-resistant stainless steel, they can withstand harsh environmental conditions, including extreme temperatures, moisture, and chemicals. This makes them an ideal choice for industrial settings, outdoor installations, and areas with high humidity or corrosive substances.
PVC cable trays, on the other hand, are lightweight and easy to install. However, they may not be as durable as stainless steel, especially in harsh environments. PVC is susceptible to UV degradation, temperature fluctuations, and certain chemicals, which can compromise its structural integrity over time.
8.2 Cost
PVC cable trays are generally more affordable than stainless steel trays. This makes them a cost-effective solution for budget-conscious projects. However, the initial cost savings may be offset by the need for more frequent replacements or repairs due to the shorter lifespan of PVC materials.
8.3 Fire Resistance
Stainless steel cable trays offer superior fire resistance. In the event of a fire, stainless steel will not melt or burn, providing a safe barrier for cables and reducing the risk of fire spread. PVC, on the other hand, is a flammable material. While PVC cable trays may be treated with fire-retardant additives, they are still not as fire-resistant as stainless steel.
8.4 Environmental Considerations
PVC is a non-biodegradable material that can release harmful chemicals during production, use, and disposal. This has raised concerns about its environmental impact. In contrast, stainless steel is a recyclable material with a lower environmental footprint.
8.5 Aesthetics
Stainless steel cable trays offer a sleek and modern aesthetic that can enhance the overall look of a facility. PVC trays, while functional, may not have the same visual appeal.
In conclusion, the choice between stainless steel and PVC cable trays depends on your specific requirements, budget, and environmental concerns. If durability, strength, and fire resistance are top priorities, stainless steel cable trays are the way to go. However, if cost is a major consideration, PVC cable trays may be a more affordable option. Ultimately, the decision should be based on a thorough analysis of your project’s unique needs and requirements.
8. Cable tray manufacturer
In the ever-evolving landscape of electrical infrastructure, the role of cable trays and cable ladders has become paramount. They serve as the backbone, supporting and organizing miles of vital cables that keep our buildings, industries, and communities functioning seamlessly. At Dosense Cable, we stand tall as a premier cable tray manufacturer and supplier, offering an extensive range of innovative solutions that cater to the diverse needs of our clients across the globe.
Being a supplier cable tray and tray cable supplier, Dosense Cable understands the importance of collaboration and customization. We work closely with our clients to understand their unique challenges and requirements, offering custom-designed solutions that seamlessly integrate into existing infrastructure. Our team of experts leverages cutting-edge technology and industry know-how to develop tailored cable trays and ladder systems that meet the highest safety standards and regulatory compliance.
Moreover, we, cable tray factory, recognize the importance of timely delivery and exceptional customer service. As a reliable cable tray and ladder supplier, Dosense Cable ensures swift order processing, efficient logistics, and round-the-clock support to our clients. Our dedicated team is always available to address any concerns or queries, ensuring a seamless experience from enquiry to installation and beyond.
In conclusion, Dosense Cable is more than just a cable tray manufacturer; we are a trusted partner in electrical cable management solutions. Our comprehensive range of cable trays and ladder systems, coupled with unparalleled customer service, sets us apart in the industry. Whether you’re a small business owner looking to streamline your office’s electrical infrastructure or a large corporation managing complex industrial facilities, Dosense Cable has the expertise and resources to deliver tailored solutions that exceed your expectations. Join us in shaping the future of electrical cable management and experience the Dosense difference today.