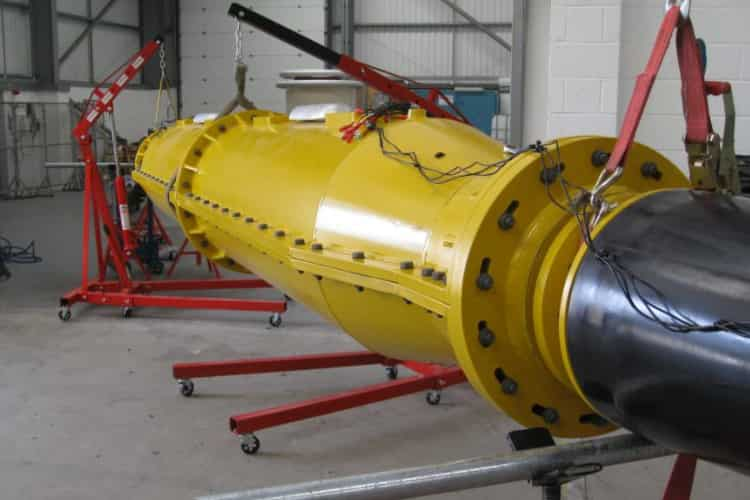
Undersøiske kabler er afgørende for moderne telekommunikation, driver global datatransmission på tværs af kontinenter og under oceaner. Disse kabler står over for adskillige udfordringer, fra miljøfaktorer til fysiske skader, necessitating robust repair and maintenance solutions. Central to this is the submarine cable joint, an essential component in maintaining and repairing these underwater communication lifelines. In this comprehensive guide, We Dosense Cable,as submarine Cable joint factory, will explore submarine cable joints, including their manufacturers, pricing, installation, and more, to give you a thorough understanding of this critical aspect of underwater infrastructure.
What is a Submarine Cable Joint?
A submarine cable joint is a specialized device used to connect or repair submarine cables, which run along the ocean floor and link different continents or islands. These cables are subject to harsh conditions, including pressure, temperature variations, and potential damage from marine activities. The joint is designed to ensure continuity and reliability in the cable’s function, providing a watertight and durable connection or repair.
Why Submarine Cable Joints are Important.
1.Continuity of Service: Submarine cable joints ensure uninterrupted data transmission by maintaining a seamless connection between cable sections.
2.Holdbarhed: These joints are engineered to withstand the harsh underwater environment, including pressure and corrosion.
3.Repair Capability: In the event of damage, cable joints allow for efficient and effective repairs, minimizing downtime.
Types of Submarine Cable Joints
Submarine cable joints come in various types, each designed to address specific needs and conditions.
Submarine cable joints come in various types, each designed to address specific needs and conditions.
1. Straight-Through Joints
Straight-through joints are used to connect two segments of the same type of submarine cable. They are straightforward in design and function, designed for extending cables or establishing new connections without altering the cable specifications.
Anvendelse: Connecting two sections of a similar submarine cable.
Design: Typically involves aligning and sealing the two cable ends.
2. Branch Joints
Branch joints are designed to divert the main cable into a new direction or branch off to connect secondary lines. These joints are more complex due to the need for additional connections and alignment.
Anvendelse: Creating branches or diversions in a submarine cable network.
Design: Includes multiple connectors and sealing mechanisms.
3. Repair Joints
Repair joints are used to fix damaged submarine cables. They restore the cable’s functionality and ensure that it can continue to transmit data reliably.
Anvendelse: Repairing damaged or broken submarine cables.
Design: Includes advanced sealing and reinforcement to address damage.
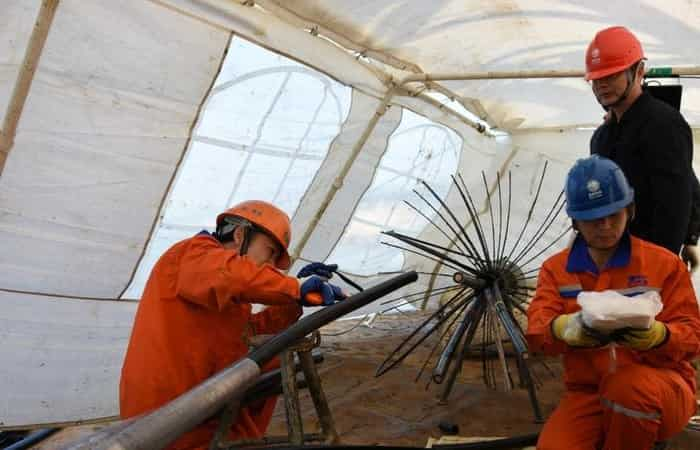
Key Components of a Submarine Joint Kit
EN submarine joint kit is a comprehensive package that includes all the components needed to assemble a submarine cable joint. These kits are essential for both installation and repair tasks. Here are the key components typically included in a submarine joint kit:
1. Joint Body
The joint body is the main structural component of the joint. It houses the cable connections and provides protection against environmental factors such as pressure and moisture.
Fungere: Houses and aligns the cable connections.
Materiale: Usually made from durable, pressure-resistant materials.
2. Sealing Elements
Sealing elements are crucial for ensuring that the joint is watertight. They prevent water ingress, which could damage the cable and degrade its performance.
Fungere: Provide a watertight seal around the cable and joint body.
Materiale: Often made from elastomers or other waterproof materials.
3. Connectors
Connectors are used to join the two cable sections or repair the damaged cable. They ensure proper electrical and mechanical connections between cable ends.
Fungere: Establish electrical connectivity between cable segments.
Design: Includes pins or terminals that match the cable’s specifications.
4. Reinforcement Materials
Reinforcement materials are used to strengthen the joint and protect it from external stresses. These materials ensure that the joint remains stable and secure under pressure.
Fungere: Provide additional strength and protection to the joint.
Materiale: Typically includes composite materials or metal reinforcements.
5. Heat Shrink Tubing
Heat shrink tubing is used to insulate and protect the joint from external elements. It shrinks when heated, forming a tight seal around the joint.
Fungere: Insulate and protect the joint from environmental damage.
Materiale: Heat-sensitive plastic that shrinks upon heating.
6. Gel or Potting Compound
Gel or potting compounds are used to fill voids within the joint, providing additional protection and insulation. These compounds help prevent water ingress and provide mechanical support.
Fungere: Fill voids and provide insulation and protection.
Materiale: Silicone-based or epoxy compounds.
Submarine Cable Joints Installation
Proper installation of submarine cable joint is essential for ensuring long-term reliability and performance. The process involves several critical steps:
1. Preparation
Preparation is key to a successful installation. This includes assessing the site, preparing the cable ends, and ensuring that all components are ready.
Site Assessment: Survey the installation area to ensure it is suitable for the joint.
Cable Preparation: Strip the insulation from the cable ends and clean them to ensure proper connection.
2. Joint Assembly
The joint is assembled according to the manufacturer’s specifications. This involves fitting connectors, sealing elements, and reinforcement materials.
Assembly: Follow the instructions to ensure that all components are correctly aligned and secured.
Testing: Perform preliminary tests to ensure that the joint is correctly assembled and that all connections are secure.
3. Deployment
The joint is deployed to its final location on the ocean floor. This requires careful handling to avoid damaging the cable or joint.
Deployment Methods: Use specialized vessels equipped with remotely operated vehicles (ROVs) or divers to position the joint.
Handling: Ensure that the joint is handled carefully to avoid physical damage.
4. Final Checks
After deployment, conduct final inspections and tests to confirm that the joint is functioning correctly and that the installation is complete.
Inspection: Check for any signs of damage or misalignment.
Testing: Perform pressure tests and functionality checks to ensure the joint is operational.
Post-Installation Activities
1.Documentation and Reporting
Document all aspects of the installation process:
Installation Report: Prepare a detailed report outlining the installation process, cable route, and any encountered issues.
As-Built Drawings: Create drawings showing the final cable route and installation details.
2.Ongoing Maintenance and Monitoring
Regular maintenance and monitoring are essential to ensure the long-term reliability of the submarine cable.
Routine Inspections: Conduct periodic inspections using ROVs or other technologies to check the condition of the cable.
Maintenance Plan: Develop a maintenance plan for addressing any potential issues and ensuring the cable remains in good condition.
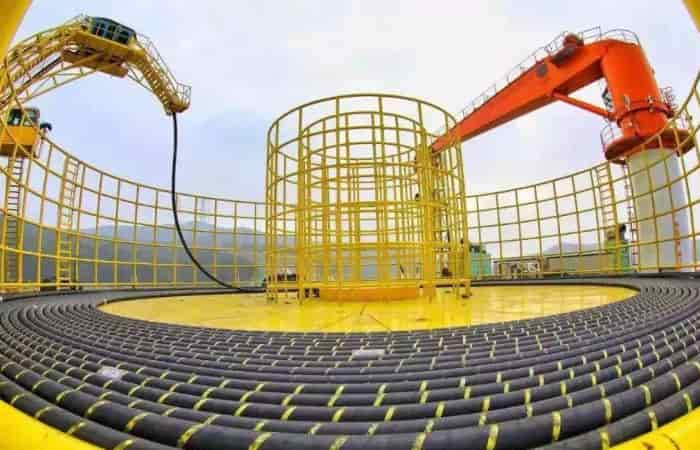
Challenges and Solutions
1 Environmental Challenges
The marine environment presents various challenges:
Strong Currents: Use advanced cable-laying techniques and equipment to manage strong ocean currents.
Seabed Obstacles: Identify and navigate around obstacles such as underwater mountains or shipwrecks.
2 Technical Challenges
Technical challenges include:
Cable Damage: Employ robust cable protection methods and conduct regular inspections to prevent and address damage.
Complex Splicing: Utilize skilled technicians and high-quality equipment to ensure accurate and reliable splicing.
How to Choose Submarine Cable joint factory and Submarine Cable Repair Company
Vi,Dosense kabel,are right company for submarine cable repairs is crucial for ensuring the reliability and efficiency of your underwater cable system. Here are some factors to consider:
1. Experience and Expertise
Choose a company with a proven track record in submarine cable joint repair. Experienced companies will have the necessary knowledge and skills to handle complex repair scenarios effectively.
2. Technology and Equipment
Ensure the company uses advanced technology and equipment for cable jointing and repair. This includes modern jointing kits, testing equipment, and deployment tools.
3. Service and Support
Consider the level of customer service and support offered by the company. Reliable service includes prompt response to emergencies, technical support, and comprehensive repair services.
4. Reputation
Check the company’s reputation in the industry by reviewing customer testimonials and case studies. A reputable company will have positive feedback from previous clients.
5. Cost and Contracts
Evaluate the cost of services and compare it with the quality and range of services provided. Long-term contracts or service agreements may offer better value and reliability.
6. Compliance and Standards
Ensure the company adheres to industry standards and regulations for submarine cable repairs. Compliance with safety and quality standards is essential for successful repairs.
Maintenance and Care for Submarine Cable Joints
Proper maintenance is essential to ensure the longevity and performance of submarine cable joints. Regular inspections and timely repairs can prevent major issues and extend the life of the cable system.
1. Routine Inspections
Conduct regular inspections of submarine cable joints to identify any signs of wear, damage, or corrosion. Routine checks help catch potential problems early and prevent larger issues.
Frequency: Schedule inspections based on the cable’s operating conditions and manufacturer recommendations.
Inspection Methods: Use remote monitoring technologies or ROVs for underwater inspections.
2. Timely Repairs
Address any issues promptly to prevent further damage. Timely repairs can prevent downtime and maintain the integrity of the cable system.
Repair Process: Follow proper procedures for repairing or replacing damaged joints.
Emergency Response: Have a plan in place for emergency repairs to minimize service interruptions.
3. Dokumentation
Keep detailed records of all inspections, repairs, and maintenance activities. This documentation helps track the cable’s condition and aids in future maintenance planning.
Records: Maintain logs of inspections, repairs, and any changes made to the cable system.
Reporting: Document any issues and actions taken to address them.
Submarine Cable Joints price
The cost of submarine cable joints can vary widely based on several factors:
1. Type of Joint
Straight-Through Joints: Generally less expensive as they involve straightforward connections without complex branching.
Branch Joints: These can be more costly due to their complexity and the need for additional components.
Repair Joints: Pricing may vary depending on the extent of damage and the complexity of the repair required.
2. Cable Specifications
The type and specifications of the submarine cable being joined or repaired significantly influence the cost. High-capacity cables with advanced features will require more sophisticated joints, affecting the overall price.
3. Fabrikant
Different manufacturers have varying pricing structures based on their technology, brand reputation, and the quality of materials used. Generally, leading brands with a reputation for reliability may command higher prices.
4. Additional Features
Joints with additional features, such as enhanced durability, advanced sealing technologies, or specialized materials, will generally be more expensive.
5. Order Quantity
Bulk purchases or long-term contracts might offer cost savings compared to individual or small-quantity orders.
Dosesne Cable,leading Manufacturers of Submarine Cable Joints
Vi,Dosense kabel, manufacturers specialize in producing submarine cable joints, each offering a range of solutions tailored to different requirements. We offer a variety of submarine cable joints designed for durability and reliability. Underwater cable jointing kits are engineered to withstand extreme underwater conditions and are used worldwide for their robust performance and advanced technology.
Vi, is renowned for its submarine cable solutions. We provide comprehensive jointing kits and repair solutions that meet stringent quality standards, ensuring long-term performance and minimal maintenance needs.
Our submarine Cable kits also solutions focus on high performance and reliability in demanding underwater environments.
Submarine Cable kits Conclusion
Submarine cable joint are integral to maintaining and repairing the vital underwater communication infrastructure that connects our world. Understanding the types of joints, førende producenter, pricing, and installation processes helps ensure that these critical components function reliably and effectively.
By selecting reputable manufacturers and repair companies, investing in high-quality jointing kits, and following best practices for installation, you can ensure the long-term performance and stability of your submarine cable systems. Whether you are dealing with a new installation or a repair situation, having a clear understanding of these elements will help you make informed decisions and maintain a robust underwater communication network.