Submarine cable
Submarine cable is a specialized type of cable designed for underwater use, generally for the purpose of transmitting electrical energy or telecommunications signals in bodies of water. Submarine cable construction is tailored to withstand the unique challenges posed by underwater environments, which include pressure, entry of water and marine life.
Subsea cables undergo rigorous testing and quality assurance procedures to ensure their reliability and performance in underwater environments.. The installation of submarine cables requires specialized vessels and equipment capable of laying and burying the cable in the seabed to minimize exposure to external risks and maintain uninterrupted operation..
Submarine cable
Submarine Electrical Cable
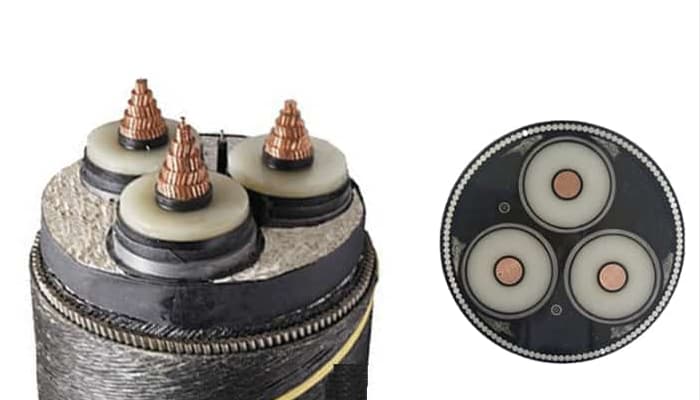
Conductor: conductor carries electrical energy or telecommunications signals. In general, It is made of copper for power transmission or optical fibers for telecommunications.
Isolation: around the driver, Insulation material prevents electrical leakage and ensures signal integrity. Common insulation materials include polyethylene, XLPE (cross-linked polyethylene) or other specialized polymers suitable for underwater use.
Metal shield and water blocking layers: in some submarine cables, the lead sheath as metal shield and water blocking layers
Water blocking layers: Multiple layers of water blocking materials are incorporated to prevent water ingress, which could compromise the performance of the cable. These layers usually include water tape or swellable materials..
Resistance members: To provide tensile strength and support the weight of the cable during installation and operation, Strength members such as aramid fibers or steel cables are integrated within the cable structure.
Armor: armored submarine cables are steel cables, to improve mechanical durability and resist damage of anchors, fishing activities or natural hazards.
External rod: Outer sheath provides additional mechanical protection and environmental resistance, protecting the cable from abrasion, corrosion and UV radiation. Materials such as polyethylene, Polyurethane or other robust polymers are commonly used for this purpose.
Cable Marino
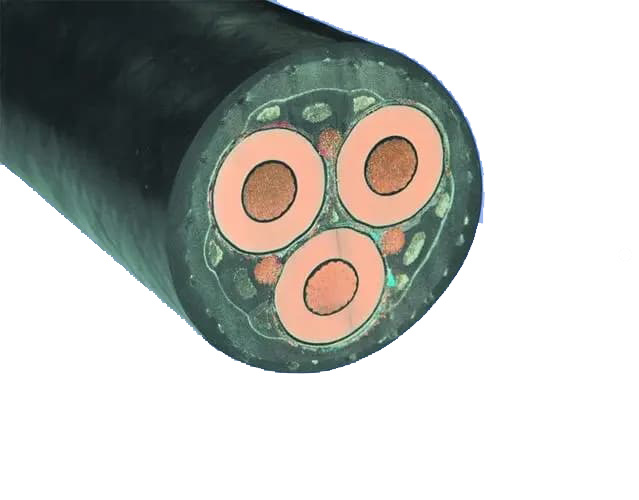
Los medium voltage marine cables They are commonly used for power transmission and distribution in marine and offshore applications.
1. Director:
Material: copper
Purpose: Conducts electrical energy at medium voltage levels.
Design: Stranded conductors for flexibility and conductivity.
2. driver shield:
Material: semiconducting layer.
Purpose: Provides a smooth interface between insulation and conductor, ensuring uniform distribution of electrical voltage.
3. Isolation:
Material: EPR, XLPE is commonly used for medium voltage cables.
Purpose: Provides electrical insulation to prevent current leakage and ensures cable integrity.
4. Isolation shield:
Material: semiconducting layer.
Purpose: Improves the distribution of the electric field and ensures a smooth transition between the insulation and the metal layers.
5. Metallic Shield:
Type: Generally a metallic layer, such as copper tape or wire braid.
Purpose: Acts as a grounding and shielding mechanism, minimizing electromagnetic interference (EMI) and providing mechanical protection.
6. Filling materials:
Purpose: Used to maintain the round shape of the cable and fill gaps between components.
7. Scotch tape:
Purpose: Holds components together and provides an extra layer of protection.
8. Metallic Shielding (Optional):
Type: Galvanized steel wires or tapes.
Purpose: Provides mechanical protection against external forces, such as crushing or impact.
9. Outer sling:
Material: Neoprene, chlorinated polyethylene, polyvinyl chloride compounds (PVC) o low smoke zero halogen compounds (LSZH).
Purpose: Protect the cable from environmental factors, abrasion and chemical exposure. LSZH is preferred for its low smoke and toxicity characteristics.
How to design submarine cable fittings and joints?
The design of a submarine cable splice involves careful consideration of several factors to ensure a reliable and durable connection between cable segments.. Here is a step-by-step guide on how to design a submarine cable joint:
Understand the requirements:
Determine the type of joint required based on the type of cable (For example, optical fiber, energy) and the specific application (For example, offshore wind farm, telecommunications network).
Consider factors such as cable diameter, driver material, the type of insulation, operating voltage/current, environmental conditions and installation method.
Select the type of joint:
Choose the appropriate gasket type based on cable specifications and installation requirements.
Prepare the cable ends:
Clean and prepare cable ends to ensure proper adhesion and electrical continuity.
Remove any contaminants, debris or damaged insulation layers from the ends of the cable using proper tools and cleaning techniques.
Conductors or Splicing Fibers:
Install gasket components:
Depending on the type of joint, assemble and install necessary components, as mechanical connectors, heat shrink tubing or resin filled casings.
Follow the manufacturer's instructions and recommended procedures for mounting and installing gaskets to ensure a good seal., adequate insulation and mechanical integrity.
Seal and isolate:
Apply sealants, adhesives or encapsulating materials to seal and insulate the joint area.
Ensure complete coverage and proper curing of sealing materials to prevent water ingress, corrosion and electrical leaks.